Will a BP knee mill handle having the table as far out as possible get damaged by pulling on the feed lever with 61 lbs force? Feed lever is 8.5"; J head.
↧
Brideport table travel vs. feed pressure
↧
eztrak programming question
hi ,i need some help programming an eztrak to mill an arc in the xz direction, im trying to mill a 3"radius 3" deep in a block of D2 USING A .6875 ball endmill , i can get it to travel with radius in correct direction .my block is 6 " wide with 0,0 in the center of part. if i can program1 line i will repeat it as many times as needed to get across
my part looks like this .
thanks
robert brintle![Click image for larger version.
Name: Barrel Vent 0 050 For Extruder.jpg
Views: 4
Size: 15.4 KB
ID: 83904]()
my part looks like this .
thanks
robert brintle

↧
↧
Hardinge Cataract QC Lathe restoration
Some of you may have seen and followed the earlier posts I had about restoring a Hardinge Cataract Quick Change Lathe back to running condition. That was Lathe #39. Well since then I've picked up another one with the serial #086. I am now in the process of restoring that one as well. This time I am posting on a Blog site the full restoration progress weekly. If you wish to view the progress you can click on the link below my name. I'll also attach a photo of the lathe as it stands at this time. I just mated the lathe bed, tray, and legs back together again. If you are reading this and own a QC lathe, or know of where one exists and have not conversed with me, I would love to hear from you. You can either PM me or email me at haroldmulder(at)hotmail.com At this time we have listed about 30 serial numbers that we believe still exist out of the approximately 300 that were built. As well I am in contact with 14 owners of these lathes. I have also heard of 5 more QC's that exist out there and am working on contacting those owners as well. Thanks for your interest in this project.
![Click image for larger version.
Name: Hardinge #86 on her legs again.jpg
Views: 4
Size: 92.6 KB
ID: 83984]()
Harold
Hardinge Cataract Blog

Harold
Hardinge Cataract Blog
↧
EZ Path 2 encoder
How does one test an encoder? The Z axis manual control no longer works. The Z axis itself works both jogging and feeding, just using the manual wheel does not work. I looked at the encoder and the wire cable is integrated with the encoder for I was hoping maybe a wire was broken. Any help? Thanks.
↧
Reverse Feed Help
I've got a problem and I know y'all can help.
The feed reverse knob assembly is broken off of my 1954 round arm/ram Bridgeport. The remaining part of the screw is recessed about 1/32" in the reverse clutch rod. Also, the reverse clutch rod seems to be flared, a little, on the end. The rod is flush with the handwheel clutch. I do not know if the reverse clutch rod is in the out, middle, or in position. Probably in.
I thought I would remove the handwheel clutch, but could not. I removed the socket set screw. Ain't there supposed to be another screw [handwheel clutch spring screw], compression spring, and 3/16 steel ball? These parts are missing. So the reverse clutch rod had no way of staying where positioned.
I can not disassemble down to the reverse clutch rod. If I could get to it I would replace it and any other things needed to be able to operate the reverse mechanism.
The handwheel clutch will not slide off of the reverse clutch rod. I took the two screws out of the feed trip bracket, thinking I could remove the whole assembly. That did not work.
Suggestions, please.
While I have your attention, I need the motor base for the motor. It is a 1hp pancake motor. I will find out tomorrow if the motor will run, I was told it did. Does any one know where I can get a used one?
I sure hope this makes sense.
Thanks for any help.
Mule
The feed reverse knob assembly is broken off of my 1954 round arm/ram Bridgeport. The remaining part of the screw is recessed about 1/32" in the reverse clutch rod. Also, the reverse clutch rod seems to be flared, a little, on the end. The rod is flush with the handwheel clutch. I do not know if the reverse clutch rod is in the out, middle, or in position. Probably in.
I thought I would remove the handwheel clutch, but could not. I removed the socket set screw. Ain't there supposed to be another screw [handwheel clutch spring screw], compression spring, and 3/16 steel ball? These parts are missing. So the reverse clutch rod had no way of staying where positioned.
I can not disassemble down to the reverse clutch rod. If I could get to it I would replace it and any other things needed to be able to operate the reverse mechanism.
The handwheel clutch will not slide off of the reverse clutch rod. I took the two screws out of the feed trip bracket, thinking I could remove the whole assembly. That did not work.
Suggestions, please.
While I have your attention, I need the motor base for the motor. It is a 1hp pancake motor. I will find out tomorrow if the motor will run, I was told it did. Does any one know where I can get a used one?
I sure hope this makes sense.
Thanks for any help.
Mule
↧
↧
Series 1 cnc quill play and tool chatter problem
I recently tried milling 7075 with a 5/8, 2 flute carbide end mill at .6 depth of cut and .2 width of cut at 30ipm on my bridgeport series 1 cnc (converted to run off mach 3). On the first pass the tool screeched so violently that current was interrupted in my limit switch circuit such that the switch was triggered. I experimented with a few different speeds and feeds, but in the end, I was forced to drop the depth of cut to .25 just so I could finish the part. I promptly called H&W machine and discussed the problem at length with a technician. I was told two possible scenarios exist: either the spindle bearings were shot or the there was play in the quill. In the past, Ive been able to deflect the endmill by hand if I push hard enough about 5 thou. This is with the quill about 3/4 the way down. When the quill is fully retracted, it is quite a bit harder to deflect the tool.
Hoping against hope that it was the spindle bearings and thus only a 300$ repair, I order the bearing kit. After installing the bearing kit this evening, the mill sounds less clackety in the spindle but the screeching problem remains. Also, with the quill at 3/4 of the way down, I can still deflect the endmill by hand about 5 though. (pushing pretty hard)
At this point, i am fairly certain there is play in the quill which causes the vibrations. However, when I run the mill with the original offending toolpath, and the screeching starts, I don't feel the vibrations on the surface of the quill. If play in the quill were the root of the problem, shouldn't I be able to feel the vibrations on the surface of the quill? Regardless, I think .005 deflection without prying is way too much!
An alternative problem I propose is the spindle taper. Is it possible that the spindle taper on my ericson quick change is worn such that the tool holder can vibrate under durress?
Thanks for any and all input!
Hoping against hope that it was the spindle bearings and thus only a 300$ repair, I order the bearing kit. After installing the bearing kit this evening, the mill sounds less clackety in the spindle but the screeching problem remains. Also, with the quill at 3/4 of the way down, I can still deflect the endmill by hand about 5 though. (pushing pretty hard)
At this point, i am fairly certain there is play in the quill which causes the vibrations. However, when I run the mill with the original offending toolpath, and the screeching starts, I don't feel the vibrations on the surface of the quill. If play in the quill were the root of the problem, shouldn't I be able to feel the vibrations on the surface of the quill? Regardless, I think .005 deflection without prying is way too much!
An alternative problem I propose is the spindle taper. Is it possible that the spindle taper on my ericson quick change is worn such that the tool holder can vibrate under durress?
Thanks for any and all input!
↧
Bridgeport 6F Table Feed Models
I have a feed stamped 6F but looks identical to an 8F. How many versions of the 6F were made ?
↧
Newbie
Hey everybody just wanted to say hello as I am a new member. I recently picked up my first Bridgeport and also a lathe. The Bridgeport is a series 1 2hp the numbers indicate a 1978 the lathe is a Maximat v-13. I will post pics as soon as I upload them I also would like some suggestions on what I would do to each machine as far as any refurbishing or refinishing. Thanks. Joe
↧
HLV-H Gear Quadrants
There appear to be three designs of change quadrant for the HLV-H. The attached scan from the sales brochure shows the three types which are described as "Metric bracket", "Inch/Metric Bracket" and "Inch bracket". The Inch bracket appears to be the one supplied as standard with imperial machines so that they can cut 10tpi.
![Click image for larger version.
Name: hlv_change_quadrants.jpg
Views: 26
Size: 50.4 KB
ID: 84667]()
It is not entirely clear what the purpose of each bracket might be. I have a metric machine and the "inch" and "metric" brackets. I'd like to cut inch (tpi) threads. Can anyone explain the differences between the quadrants and which one is used for which purpose?
Alan

It is not entirely clear what the purpose of each bracket might be. I have a metric machine and the "inch" and "metric" brackets. I'd like to cut inch (tpi) threads. Can anyone explain the differences between the quadrants and which one is used for which purpose?
Alan
↧
↧
Problems to send home axis in hardinge Cobra 51
Hi guys.
Someone can helpme ?
Machine hardinge Cobra 51
Fanuc 16 M
I have a problem becose the batery encoder lost.
I changue the batery and don can recovery the position home becose the encoder is absolute.
The form of send to home is G28 X0 Z0 , when I send to home in MdI the axis is moved but the machine going to over travel.
I make the procedure manual fanuc Parameter 1815 and this make the same.
Someone can helpme ?
Machine hardinge Cobra 51
Fanuc 16 M
I have a problem becose the batery encoder lost.
I changue the batery and don can recovery the position home becose the encoder is absolute.
The form of send to home is G28 X0 Z0 , when I send to home in MdI the axis is moved but the machine going to over travel.
I make the procedure manual fanuc Parameter 1815 and this make the same.
↧
Bridgeport Interact remove head
Hi Guys, hope someone here can help. Ive just managed to purchase a Bridgeport interact series 1 from a friend, I now need to move this into my workshop. The problem comes as I need to squeeze the mill under a 5ft opening. To do this I was planning on rem removing the head. I plan to remove the complete head as one unit with an engine hoist. Is this a straightforward job, or are there lots of gotchas to worry about? Ive had a look for videos of it being doing, but have had no luck with finding one for a non j-type head, as the head on the interact is fixed. Any help would be magic.
Thanks
Jim
Thanks
Jim
↧
SV 200 Lathe Spindle Bearings
My SV 200 Lathe has started making noise in the spindle area, I'm leaning to the spindle bearings.
I know Hardindge has some maintenance procedures on how to do stuff like changing the spindle bearings. Also a parts list would be helpful. But you can't get ahold of anyone to talk to at Hardinge anymore.
If anyone has any suggestions it would be greatly appreciated.
Thanks, Jim
I know Hardindge has some maintenance procedures on how to do stuff like changing the spindle bearings. Also a parts list would be helpful. But you can't get ahold of anyone to talk to at Hardinge anymore.
If anyone has any suggestions it would be greatly appreciated.
Thanks, Jim
↧
Bridgeport table slack
Hey Guys,
It has become quite evident on a job we are currently doing that the side to side slack on our Bridgeport BR J turret mill is getting to bad. I have had many machines in bits over the years but never a Bridgeport. How easy is it to take up the slack on the lead screw and how should I go about doing it.
Cheers,
Pete
It has become quite evident on a job we are currently doing that the side to side slack on our Bridgeport BR J turret mill is getting to bad. I have had many machines in bits over the years but never a Bridgeport. How easy is it to take up the slack on the lead screw and how should I go about doing it.
Cheers,
Pete
↧
↧
Hardinge Assembly Identification
Need a little assist in trying to ID a Hardinge assembly and one other piece.
I know the feed and cross feed assembly is a Hardinge part, but it has no other identifying
marks except the number 4 and that isnt under the logo.
![Click image for larger version.
Name: DSC_0002.jpg
Views: 34
Size: 41.7 KB
ID: 84811]()
![Click image for larger version.
Name: DSC_0001.jpg
Views: 31
Size: 40.4 KB
ID: 84810]()
![Click image for larger version.
Name: DSC_0004.jpg
Views: 30
Size: 40.4 KB
ID: 84809]()
![Click image for larger version.
Name: DSC_0003.jpg
Views: 27
Size: 41.8 KB
ID: 84812]()
The pics of the other assembly has no markings except the number 4 stamped on the upper and lower slides. The unmarked assembly appears to be a boring feed (?) of some sort.
I'll attach the other 2 pics in the next post
Any help appreciated,
Thanks
Dick
I know the feed and cross feed assembly is a Hardinge part, but it has no other identifying
marks except the number 4 and that isnt under the logo.




The pics of the other assembly has no markings except the number 4 stamped on the upper and lower slides. The unmarked assembly appears to be a boring feed (?) of some sort.
I'll attach the other 2 pics in the next post
Any help appreciated,
Thanks
Dick
↧
Bridgeport motor - 4 speed with shifter
Has anyone seen a motor like this on a Bridgeport mill? I've been searching on this site and other places online, and have not seen anything. It was made by Lima drives in Lima Ohio. I contacted them, and they have no info either. I'ts way simpler than changing the belt and pulley.
↧
Mill ID help
Hello,
I picked up a mill yesterday and it's a bit of a mystery. The owner said that years ago, the head of his Bridgeport locked up so he replaced it with the head off of a Millport. Although the mill body is in good condition, I'm questioning if it is indeed a Bridgeport body. The only markings (clues) on it is a safety sticker from Enco. Did all Bridgeports have the logo cast into the arm? Here are a few photos.
![Click image for larger version.
Name: bridgeport2.jpg
Views: 47
Size: 100.4 KB
ID: 84928]()
![Click image for larger version.
Name: bridgeport1.jpg
Views: 44
Size: 94.7 KB
ID: 84929]()
Thanks for any help,
Jack
Fort Loramie, Ohio
I picked up a mill yesterday and it's a bit of a mystery. The owner said that years ago, the head of his Bridgeport locked up so he replaced it with the head off of a Millport. Although the mill body is in good condition, I'm questioning if it is indeed a Bridgeport body. The only markings (clues) on it is a safety sticker from Enco. Did all Bridgeports have the logo cast into the arm? Here are a few photos.


Thanks for any help,
Jack
Fort Loramie, Ohio
↧
Need to learn how to use Bridgeport with digital readout and Harrison AA Lathe
:willy_nilly: This may sound different. I will be 75 this Dec, my friend is 6 mos older than I.
Both of us are decent woodworkers with woodworking machine experience. One of his
wonderful sons gave him a Bridgeport milling machine w/digital readout, he has a good old
Harrison AA Lathe. We both can play and do basic things with the tools, but he has heard
that there are books CD-s available that can teach him the basics of machining. We are
getting to be not as fast on the uptake as we once were-:nono:-and are going to have to
take this at our own speed. The wife has her custom bathroom with soaking tub and the
custom quatersawn white oak kitchen and we need something to keep us out of trouble and
off streetcorners. Can anyone recommend some learning tools. Thank you for any help you
can give us.
Both of us are decent woodworkers with woodworking machine experience. One of his
wonderful sons gave him a Bridgeport milling machine w/digital readout, he has a good old
Harrison AA Lathe. We both can play and do basic things with the tools, but he has heard
that there are books CD-s available that can teach him the basics of machining. We are
getting to be not as fast on the uptake as we once were-:nono:-and are going to have to
take this at our own speed. The wife has her custom bathroom with soaking tub and the
custom quatersawn white oak kitchen and we need something to keep us out of trouble and
off streetcorners. Can anyone recommend some learning tools. Thank you for any help you
can give us.
↧
↧
New machine day
I helped my good buddy Gill move his newly purchased Bridgeport mill this weekend. We had a nice country drive through southeast Alabama for a few hours. It was a beautiful area, and new places I have never been before.
Someone else I know contacted me about a relative who had passed away and he was going to buy a Southbend lathe, but there was also a nice Bridgy for sale too. I told Gill about it and they both struck a deal.
The mill is a great shape, and included the original vise, collets and drill chuck, rotory phase converter, and a Mitutoyo digital readout.
I of course had to use my Gopro and film our machine moving adventure. :D
Hope you guys enjoy.
Someone else I know contacted me about a relative who had passed away and he was going to buy a Southbend lathe, but there was also a nice Bridgy for sale too. I told Gill about it and they both struck a deal.
The mill is a great shape, and included the original vise, collets and drill chuck, rotory phase converter, and a Mitutoyo digital readout.
I of course had to use my Gopro and film our machine moving adventure. :D
Hope you guys enjoy.
↧
BP Clone: WTF is this control for ???
I hope Bridgeport clones aren't off-topic....
Can anyone help me figure out what this control is for? I've only had my (new to me) mill up and running to test the VFD, but I wasn't able to see any difference when changing this control from one position to the next. The icons for the control aren't making things any clearer for me. In case you can't read the words, it says "Stop Spindle Before Shifting".
![]()
A toast to whoever comes up with the correct answer and another toast to whoever comes up with the most bizarre answer. :crazy:
Can anyone help me figure out what this control is for? I've only had my (new to me) mill up and running to test the VFD, but I wasn't able to see any difference when changing this control from one position to the next. The icons for the control aren't making things any clearer for me. In case you can't read the words, it says "Stop Spindle Before Shifting".
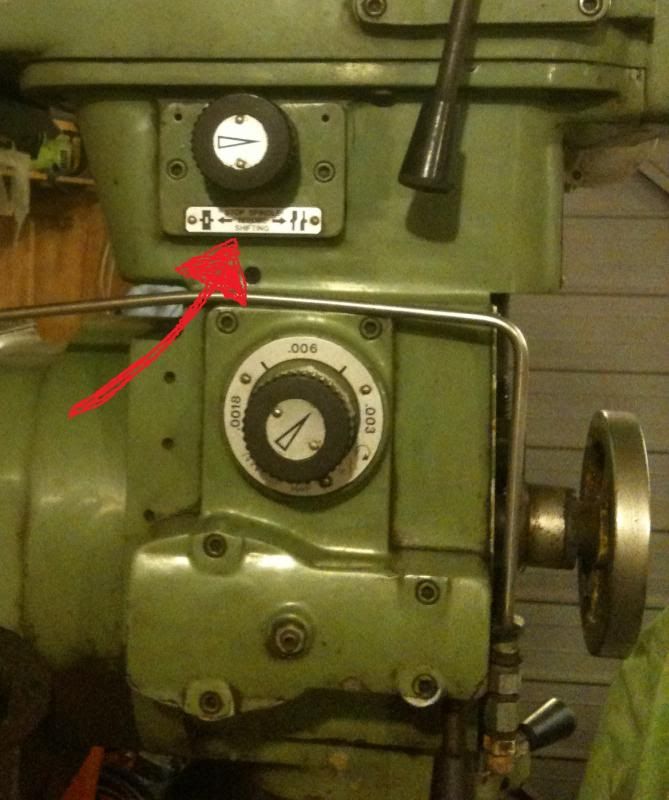
A toast to whoever comes up with the correct answer and another toast to whoever comes up with the most bizarre answer. :crazy:
↧
Hardinge HLVH vs HC
What makes the hlvh so much more expensive than the hc?! What am I missing? I see used HlVH's for sale for 15-25k. Chuckers for 2-7k. Why?
↧